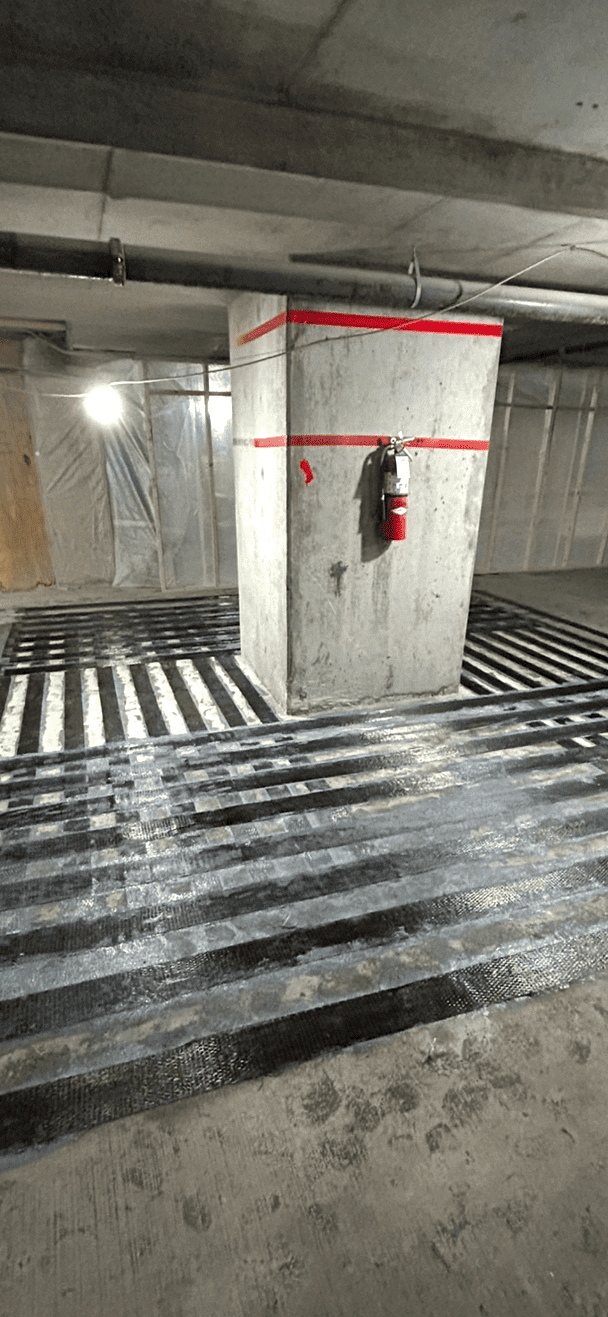
Timely, well-executed concrete repairs are essential to keeping parking garages safe and fully operational. Delays can create major disruptions for employees and visitors, while unanticipated structural issues can quickly escalate costs. Addressing repairs thoroughly the first time is critical to preventing long-term damage and unnecessary future expenses.
When HCA needed repairs for its seven-story parking structure, Parman Parking Garage, they turned to Charter Construction. Known as one of Nashville’s most trusted concrete experts, Charter was selected because of the ability to handle complex repairs with precision and efficiency. As an assistant project manager for Charter, Hank Arnold has served as a repair specialist on numerous projects. He offered an inside look at how the team approached this large-scale repair project.
“Concrete damage is never going to get better on its own,” Hank said. “Taking a proactive approach can save significant time and money in the long run.”
HCA proactively initiated the repair project after noticing visible signs of deterioration, including rust stains, spalled concrete, and exposed reinforcement. They reached out to Pivot Engineers & Structural Design Group (SDG) for an initial assessment, and Robins & Morton was selected to serve as the general contractor. After reviewing the findings and leading the RFP process, Robins & Morton selected Charter to lead the concrete restoration work.
A Detailed Approach for Assessing Repairs
With any concrete repair project, a comprehensive assessment is key to ensuring that all structural issues are identified and addressed completely. The goal is to avoid partial repairs that could lead to additional problems in the future. To achieve this, Charter conducted an in-depth site survey to match the estimated budget with actual on-site conditions.
As part of this assessment, the team compiled an interactive survey of the entire garage, capturing over 1,300 photos to document existing damage.
“We took a meticulous approach to ensure that every necessary repair was identified,” Hank shared. “Our goal was to deliver a complete solution that would extend the life of the structure and prevent future issues.”
This detailed visual record provided the design team and general contractor with a valuable tool to track repairs and plan accordingly.
Executing Meticulous Repairs with Precision
The nature of this project presented unique challenges, particularly because the garage was a pre-cast structure. Standard repair approaches had to be adjusted to accommodate unique aspects of the garage. Chris O’Neill served as the on-site quality control manager, ensuring that every repair met the project’s design criteria. His oversight played a critical role in maintaining efficiency and maximizing material use.
“When the concrete is thinner, you don’t want to place a lot of repair material at once. In this instance, we had to hand-apply concrete into the repair cavities.”
A key highlight of this project was the Charter team’s ability to maximize efficiency and accelerate the schedule. While full-depth saw-cutting is a standard method for slab repairs, Charter identified a notable efficiency boost during execution. Leveraging this advantage, the team proposed converting soffit repairs over three square feet to full-depth repairs. This strategic adjustment optimized workflow, enabling Charter to meet the project’s demanding timeline without compromising quality or cost-effectiveness.
The field crew completed an extensive number of repairs—covering the entire 270,000-square-foot garage—in just eight months.
Superintendent Jose Rodriguez led the field team, ensuring the job remained on schedule while maintaining the highest quality standards. The field team’s commitment to the project was evident, with foremen often working alongside crew members to complete the repairs.
“Jose did an incredible job leading the crew to meet the client’s schedule demands while keeping the project on budget,” Hank said.
Addressing all structural issues upfront quickly and completely helped extend the life of HCA’s parking structure for decades, providing HCA with a durable and long-lasting solution.
“By tackling these repairs thoroughly now, we’ve helped HCA avoid larger structural issues down the road,” Hank said. “It’s always rewarding to see a project come together in a way that benefits the client for years to come.”